The form has been successfully submitted.
Please find further information in your mailbox.
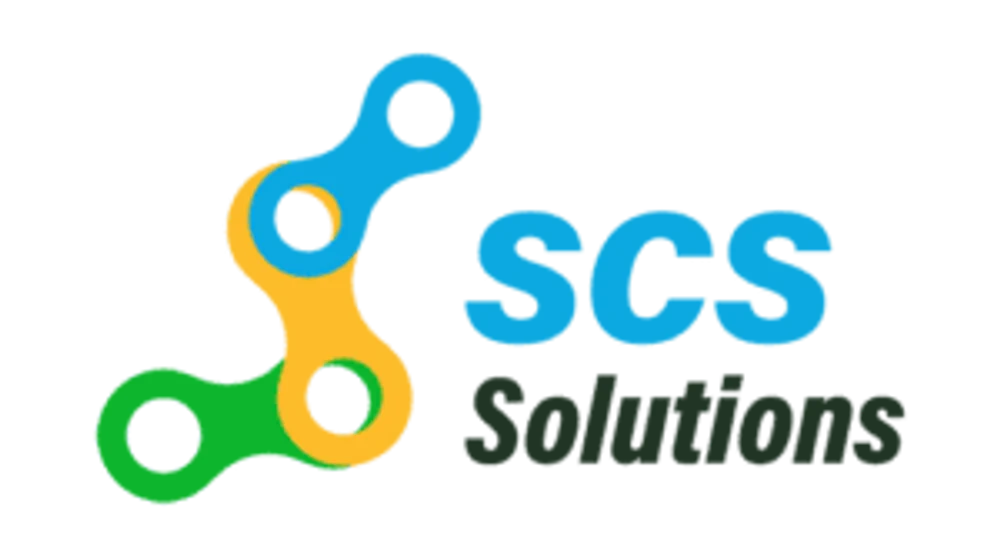
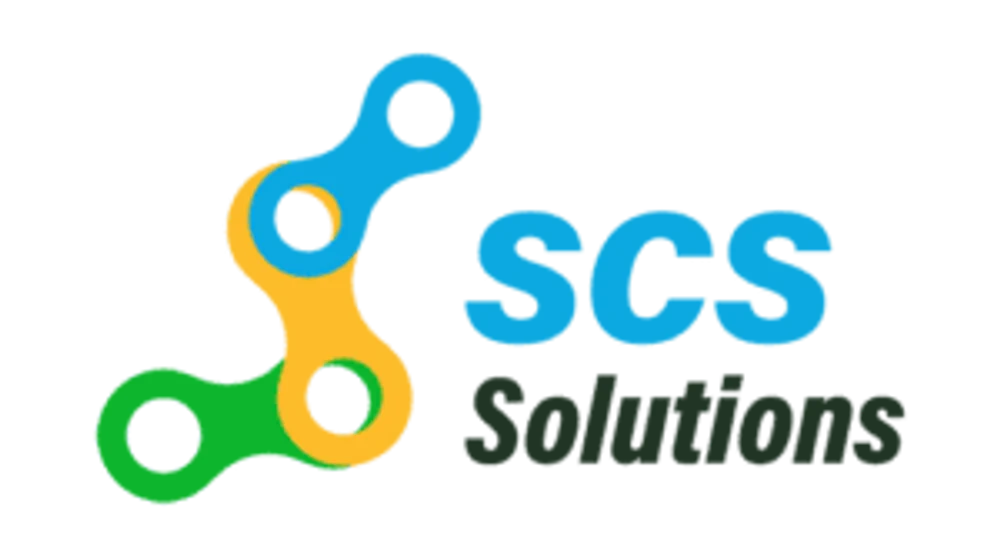
What Is a Warehouse Management System (WMS)?
Author:
SCS
Published: Jun 1, 2023
|Updated: Jun 4, 2024
Table of Contents
Are you running a warehouse and feeling overwhelmed by the amount of inventory you need to manage? Are you struggling to keep track of stock levels, shipping and receiving, and overall warehouse operations? If so, it's time to consider implementing a Warehouse Management System (WMS).
1. Define Warehouse Management System
Warehouse management is a crucial component of supply chain management. A Warehouse Management System (WMS) is software designed to manage and optimize warehouse operations. It is used to manage inventory, order fulfillment, receiving and putting away, shipping and tracking, and reporting and analytics. WMS is an essential tool for businesses that manage large quantities of products and need to maintain accurate inventory records.

2. What are the critical features of WMS?
A WMS has several key features that make it an essential tool for warehouse management:
2.1 Inventory Management
A WMS provides real-time tracking of inventory levels and locations, allowing warehouse managers to optimize space utilization and minimize stockouts. Inventory management features include product tracking, cycle counting, and automated replenishment.
2.2 Order Fulfillment
Warehouse Management System streamlines order fulfillment by automating picking and packing processes. It helps ensure accurate order picking and reduces the time required for order fulfillment.
2.3 Receiving and Putaway
WMS helps warehouse staff manage the receiving and putaway processes, from scheduling deliveries to locating and storing products in the correct location. This helps to improve accuracy and reduce the time required for these processes.
2.4 Shipping and Tracking
WMS simplifies the shipping process by automating shipping label generation, package tracking, and carrier selection. It provides real-time tracking information to both warehouse staff and customers, ensuring transparency and accountability.
2.5 Reporting and Analytics
WMS provides insights into warehouse operations through real-time reporting and analytics. It helps warehouse managers make informed decisions by providing key performance indicators (KPIs) such as inventory turnover, order fulfillment rates, and warehouse capacity utilization.
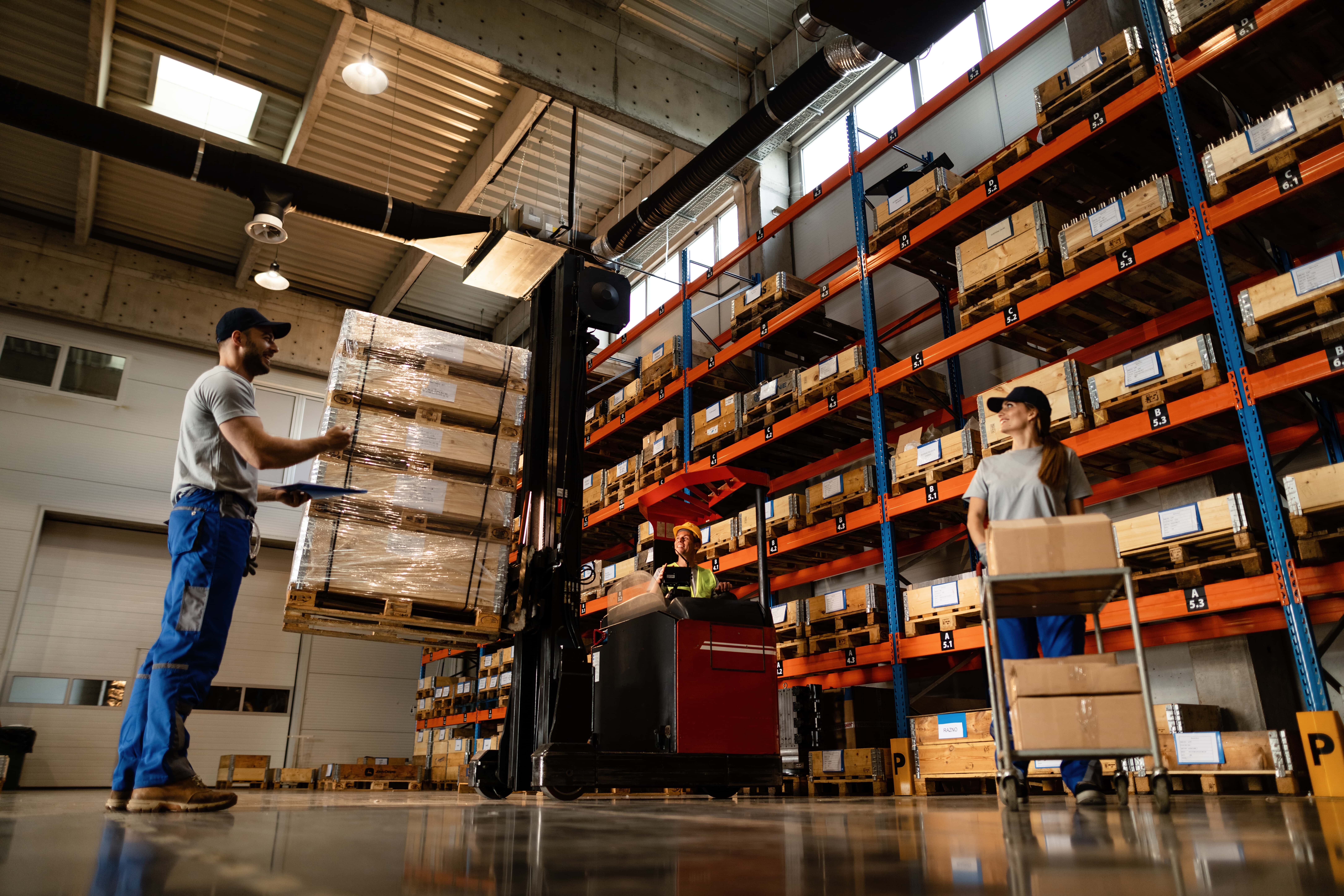
3. What are the benefits of WMS?
There are several benefits of using a Warehouse Management System in warehouse operations:
3.1 Increased Efficiency and Productivity
WMS streamlines warehouse operations by automating many manual processes. This reduces the time required for tasks such as inventory management, order fulfillment, and shipping, allowing warehouse staff to focus on higher-value activities.
3.2 Improved Accuracy and Inventory Control
WMS provides real-time tracking of inventory levels and locations, reducing the likelihood of stockouts and overstocking. It also improves the accuracy of order picking and shipping, reducing the risk of errors and increasing customer satisfaction.
3.3 Real-time Tracking and Visibility
WMS provides real-time data on inventory levels, order status, and shipping information. This allows warehouse managers to quickly identify issues and make informed decisions.
3.4 Better Customer Service
WMS enables faster order fulfillment and provides real-time tracking information to customers, improving customer satisfaction and loyalty.
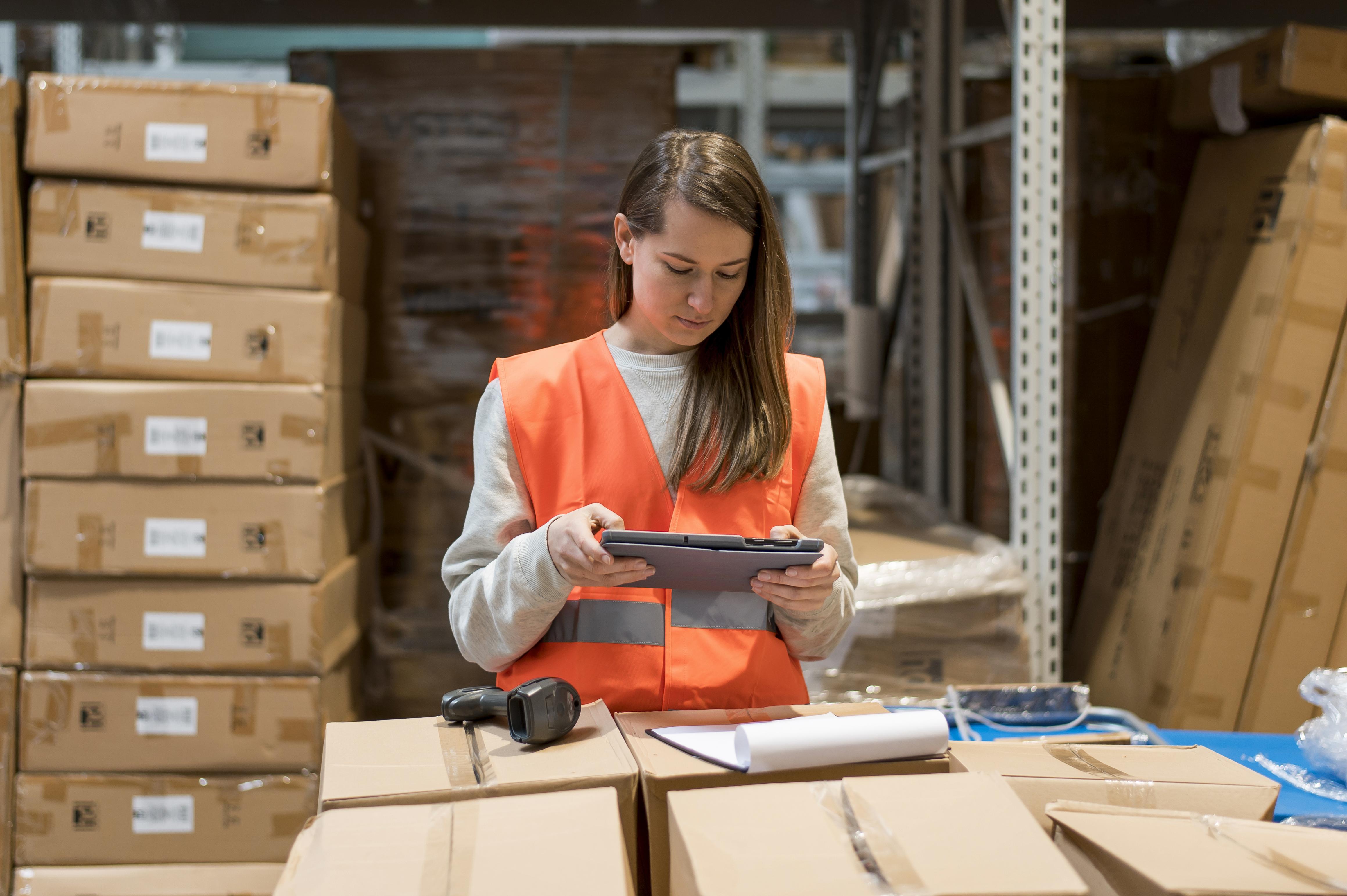
4. How are we choosing the right WMS?
Choosing the right WMS for your business is essential. Here are some factors to consider when evaluating WMS options:
4.1 Understanding Your Business Needs
Identify your warehouse's specific needs and priorities, such as inventory management, order fulfillment, or shipping. This will help you choose a WMS that is tailored to your business.
4.2 Evaluating System Capabilities
Evaluate WMS systems based on their functionality, ease of use, and scalability. Look for a system that can accommodate your current needs and grow your business.
4.3 Cost Considerations
Consider the upfront and ongoing costs of implementing a Warehouse Management System. This includes the cost of software licenses, hardware, implementation, and ongoing maintenance.
4.4 Integration with Existing Systems
Choose a WMS that can integrate with your existing ERP, transportation management, and other systems to streamline operations and reduce data entry errors.

5. How is the future of WMS?
WMS is continually evolving with advances in technology. Here are some trends that are shaping the future of WMS:
5.1 Advancements in Technology
New technologies such as artificial intelligence and the Internet of Things (IoT) are being integrated into WMS to improve automation and efficiency.
5.2 Integration with Other Systems
WMS is becoming more integrated with other systems such as transportation management and ERP, providing end-to-end visibility and control over the entire supply chain.
5.3 Expansion of E-commerce
The growth of e-commerce is driving demand for more sophisticated Warehouse Management System that can handle complex order fulfillment processes, such as pick and pack, multi-channel shipping, and returns management.
SCS - All-in-one solution for your digital transformation.
Contact us today to schedule a demo and unlock new opportunities for growth!
Share:
Related Post
View More Related ArticlesCloud-Based Warehouse Management System: A Game-Changer
A cloud-based warehouse management system empowers you to take advantage of this secret weapon, optimizing operations, and getting ahead of the competition.
17 Must-have e-commerce app features to boost your business success
Are you looking to make a mark in the competitive eCommerce market? Here’s a comprehensive list of the must-have features for your eCommerce app to ensure seamless user experiences, increased sales, and loyal customers.
What is inventory demand forecasting? Why is inventory demand forecasting crucial for manufacturing businesses?
Inventory demand forecasting is a critical process for manufacturing businesses. In this comprehensive guide, learn what inventory demand forecasting is and why it is crucial for optimizing operations and driving business success. Discover the benefits of accurate demand forecasting, such as minimizing stockouts, reducing carrying costs, and improving customer satisfaction. Gain valuable insights into the various methods and tools used in inventory demand forecasting and how they can be applied to enhance decision-making and supply chain management in the manufacturing sector.
Cloud-Based Warehouse Management System: A Game-Changer
A cloud-based warehouse management system empowers you to take advantage of this secret weapon, optimizing operations, and getting ahead of the competition.
17 Must-have e-commerce app features to boost your business success
Are you looking to make a mark in the competitive eCommerce market? Here’s a comprehensive list of the must-have features for your eCommerce app to ensure seamless user experiences, increased sales, and loyal customers.
What is inventory demand forecasting? Why is inventory demand forecasting crucial for manufacturing businesses?
Inventory demand forecasting is a critical process for manufacturing businesses. In this comprehensive guide, learn what inventory demand forecasting is and why it is crucial for optimizing operations and driving business success. Discover the benefits of accurate demand forecasting, such as minimizing stockouts, reducing carrying costs, and improving customer satisfaction. Gain valuable insights into the various methods and tools used in inventory demand forecasting and how they can be applied to enhance decision-making and supply chain management in the manufacturing sector.
Table of Contents
(Hide)
Contact us!
Book a call or fill out the form below and we’ll get backto you once we’ve processed your request.
What happens next?
Having received and processed your request, we will get back to you shortly to detail your project needs and sign an NDA to ensure the confidentiality of information.
After examining requirements, our analysts and developers devise a project proposal with the scope of works, team size, time and cost estimates.
We arrange a meeting with you to discuss the offer and come to an agreement.
We sign a contract and start working on your project as quickly as possible.
Let●s develop
software together!
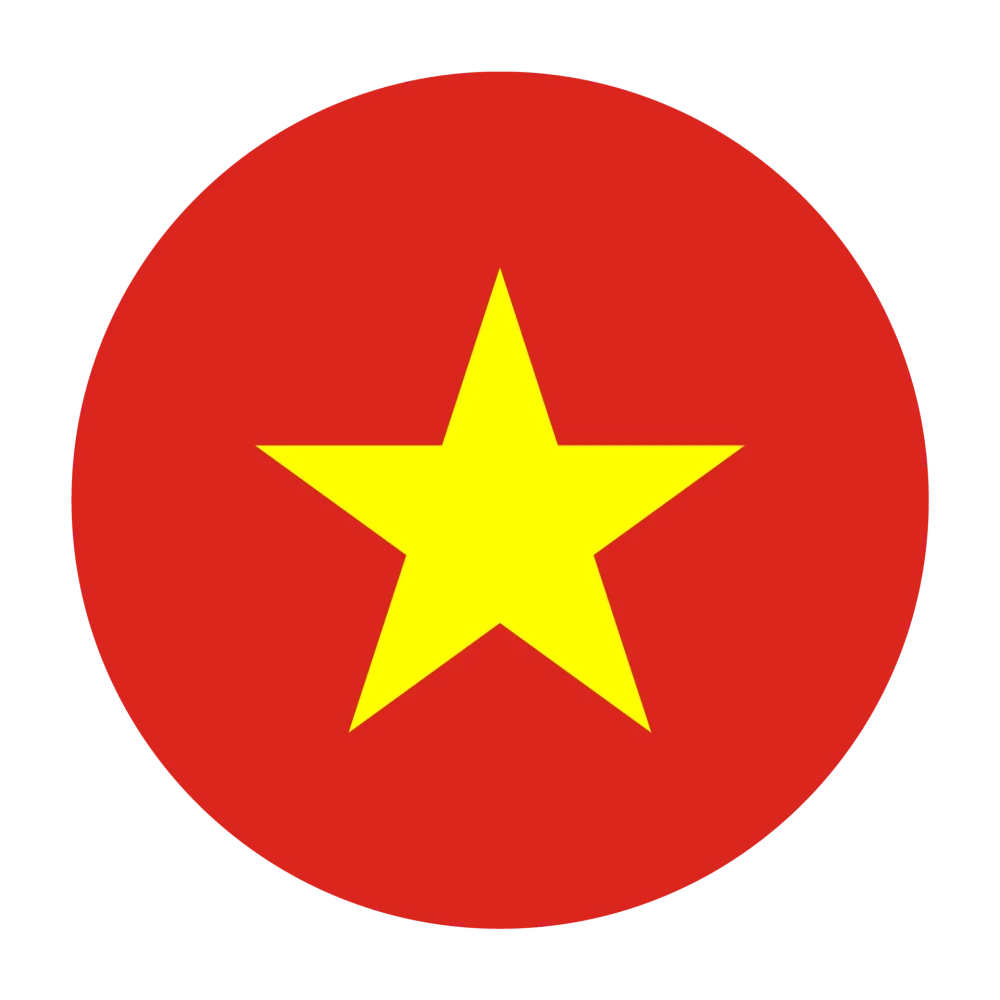
Floor 3, 40/4 Lam Son Street, Ward 2, Tan Binh district, Ho Chi Minh City.
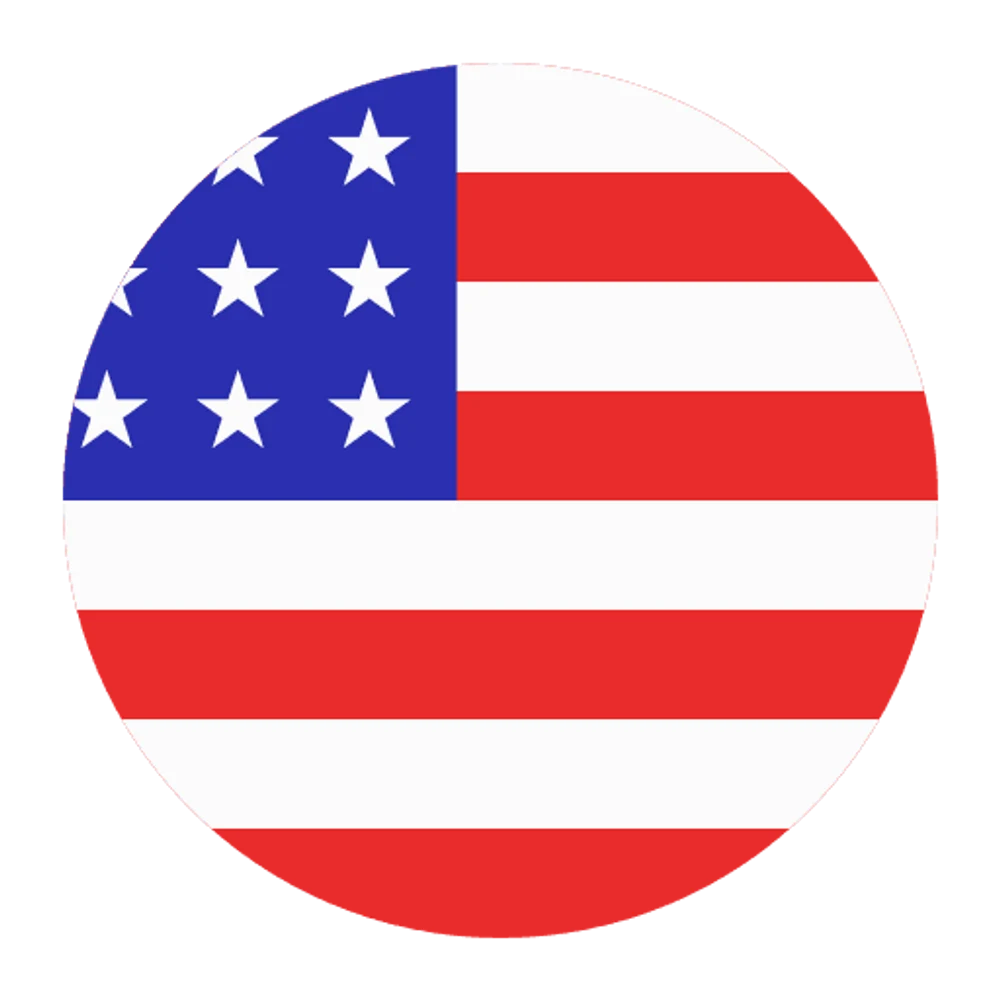
1160 Alum Creek Dr, Columbus, OH 43209
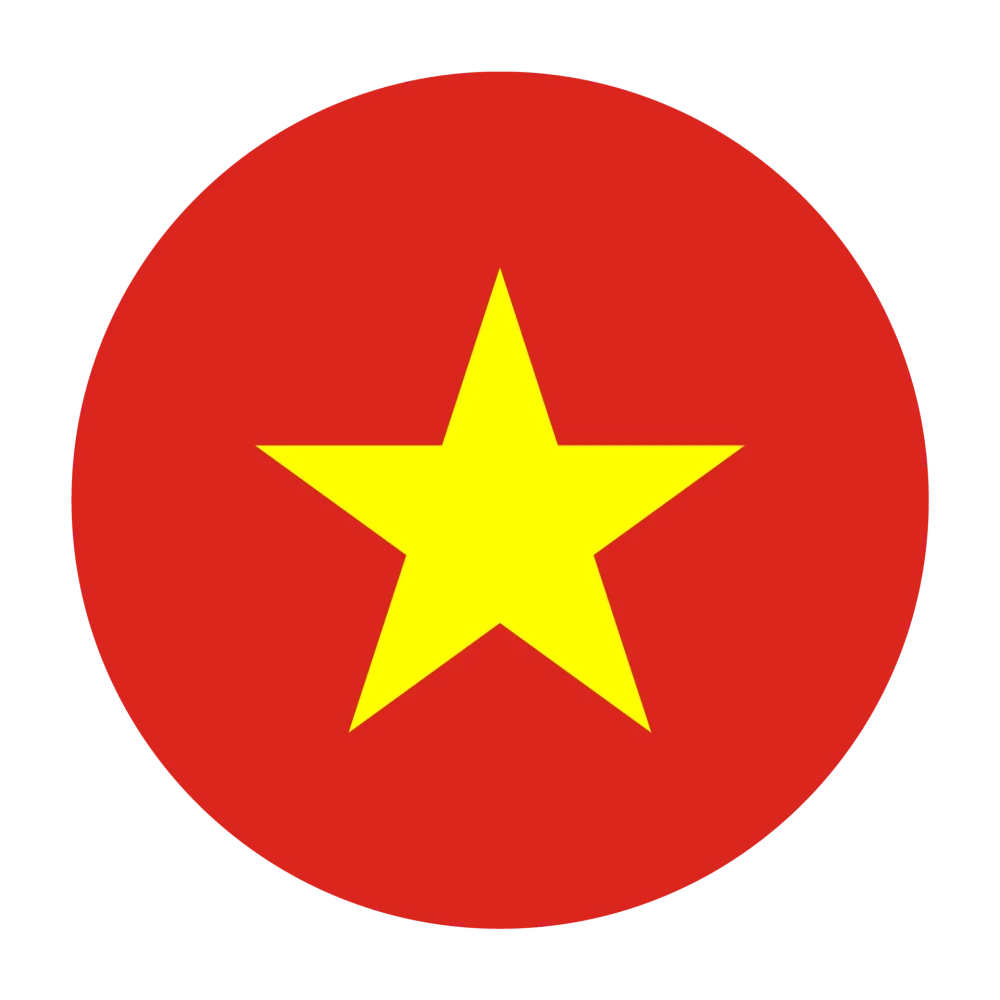
Floor 3, 40/4 Lam Son Street, Ward 2, Tan Binh district, Ho Chi Minh City.
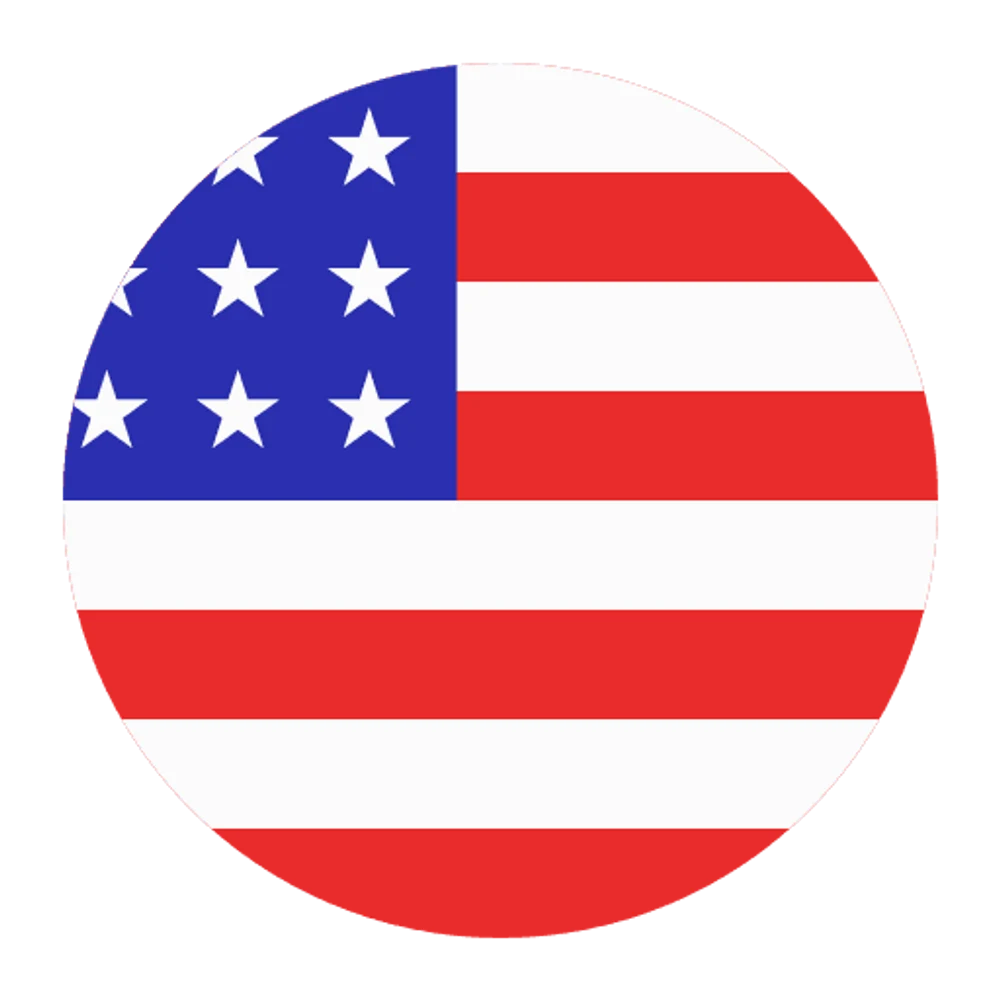
1160 Alum Creek Dr, Columbus, OH 43209